Comprehensive Overview of Industrial 3D Scanning Sensors
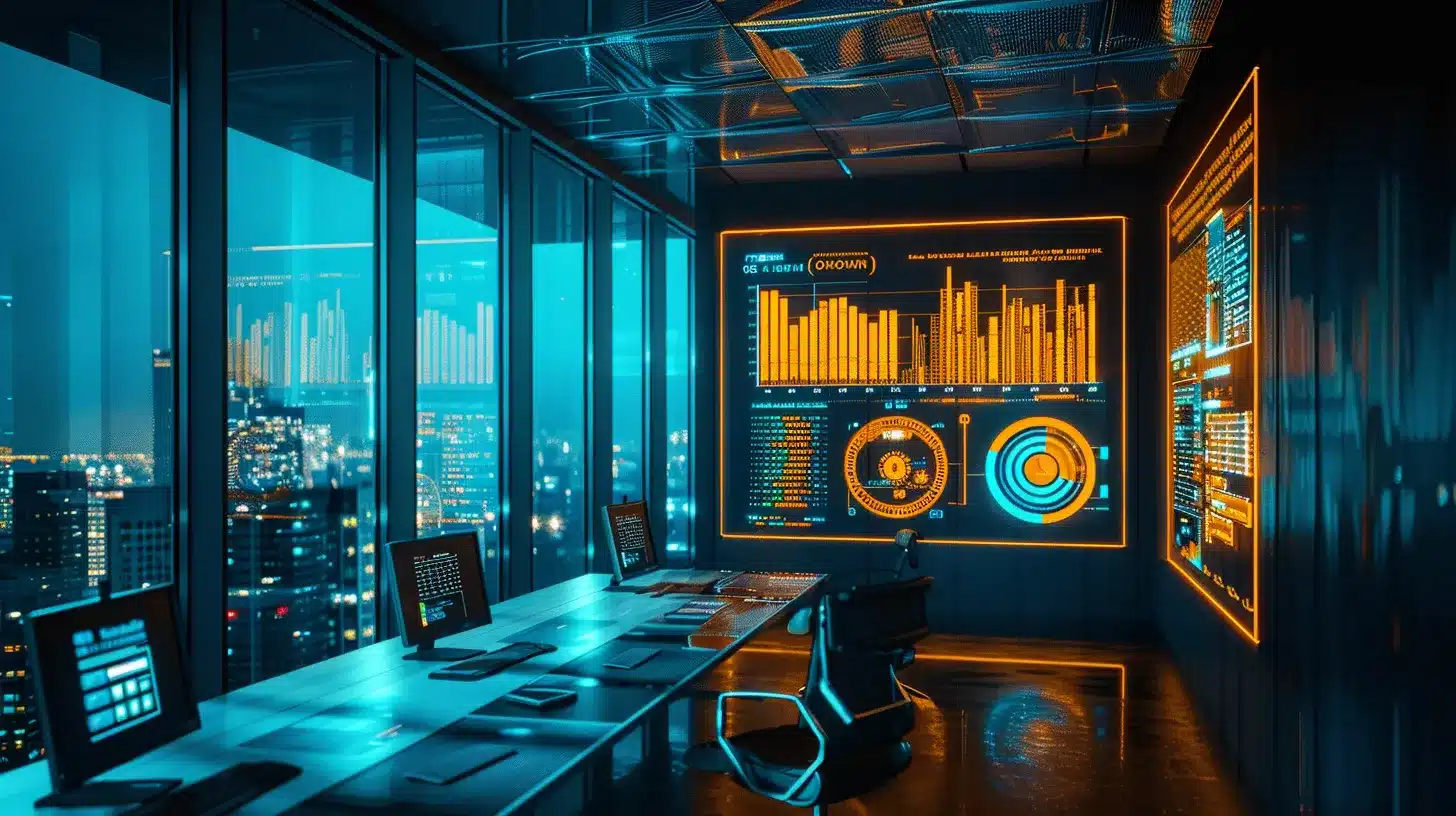
Industrial 3D Scanning Sensors: What You Need to Know
Industrial 3D scanning sensors are transforming how businesses approach measurement and quality control. With various types available, such as laser and structured light scanners, understanding these tools can significantly enhance operational efficiency. This article will cover the key functions and types of industrial 3D scanning sensors, their applications across industries, and guidance on selecting the right sensor for specific needs. Readers will discover how these technologies can streamline their processes, addressing common challenges in accuracy and precision while staying competitive in the market.
Key Takeaways
- Industrial 3D scanning sensors enhance precision in measurements and modeling across various industries
- Automation in scanning processes significantly improves workflow efficiency and reduces human error
- Real-time inspection capabilities lead to better quality control and increased customer satisfaction
- The integration of AI and advanced algorithms enhances data processing and decision-making efficiency
- Selecting the right sensor involves evaluating performance characteristics and specific industry needs
Understanding Industrial 3D Scanning Sensors and Their Functions

Industrial 3D scanning sensors serve as essential tools for capturing precise measurements and creating detailed 3D models of objects. This section covers the key components of 3D scanning systems, highlighting their roles in enhancing workflow and improving quality control. An explanation of how these sensors operate will emphasize their impact on efficiency and quality assurance in various industries.
Definition of Industrial 3D Scanning Sensors
Industrial 3D scanning sensors are sophisticated devices designed to capture accurate geometric data from physical objects, enabling the creation of detailed three-dimensional models. These sensors play a critical role in various applications, including reverse engineering, where precision measurement is vital for replicating complex gear systems. By leveraging mobile devices integrated with these sensors, industries can achieve greater automation and efficiency in their workflows, ensuring high-quality outputs that meet rigorous standards.
Key Components of 3D Scanning Systems
Industrial 3D scanning systems comprise several key components that contribute to effective data acquisition. At the core of these systems, 3D scanning sensors utilize structured light and laser technology to measure angles and distances accurately, ensuring high-resolution models are created for applications such as metrology. Additionally, the integration of mobile devices enhances the portability of these machines, allowing for versatile scanning setups and improved workflow efficiency.
How Industrial 3D Scanning Sensors Work
Industrial 3D scanning sensors operate by emitting structured light or laser beams that capture the dimensions of physical objects, resulting in a point cloud that represents the object’s geometry. This data is processed using specialized software to create detailed STL models, which are essential for applications requiring high levels of detail, such as prototyping and quality assurance. By improving productivity through rapid data acquisition and accurate modeling, these sensors streamline workflows and support better decision-making in various manufacturing and engineering contexts.
Types of Industrial 3D Scanning Sensors
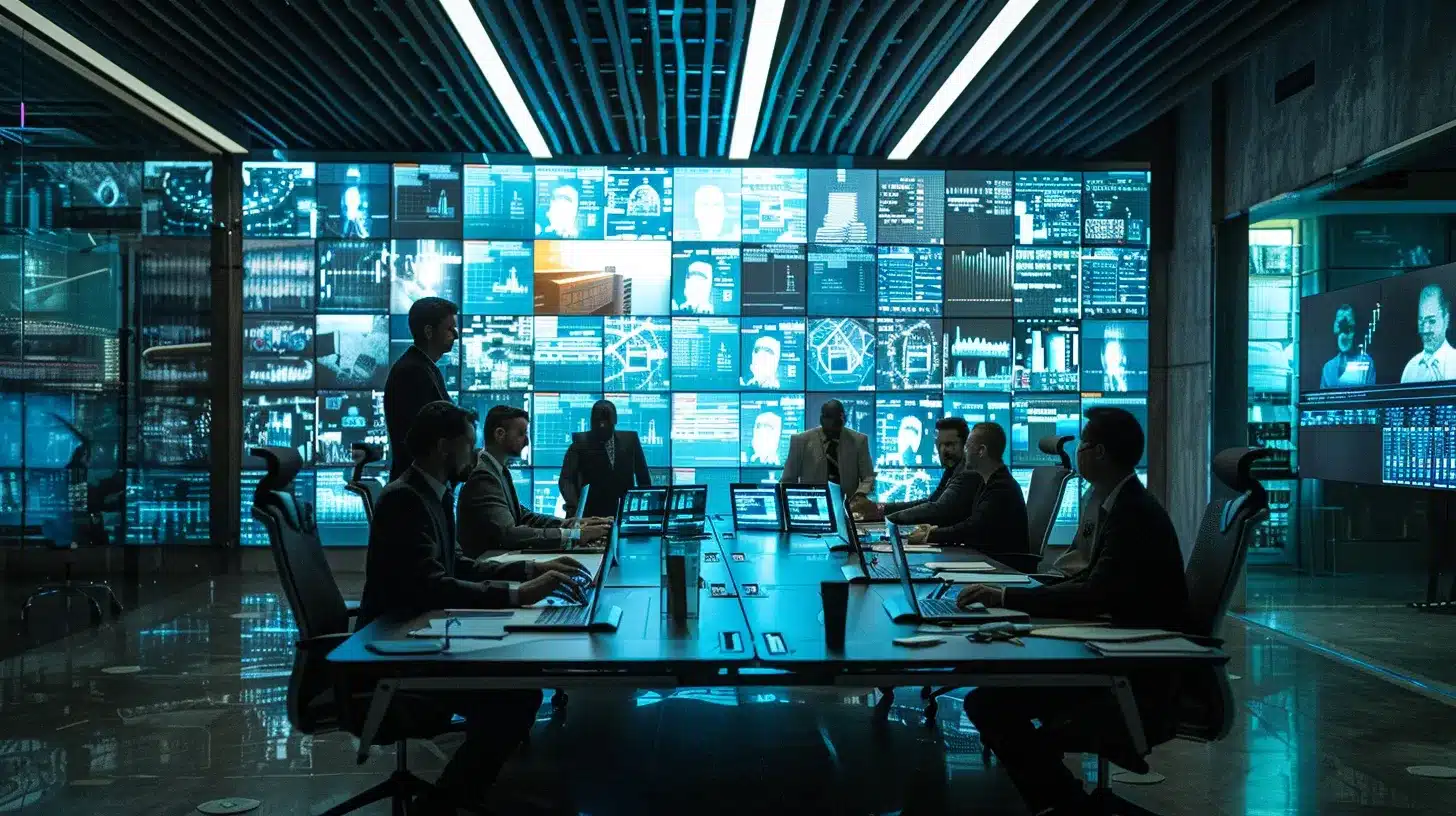
In the realm of industrial 3D scanning sensors, understanding the various types is crucial for effective machine vision and 3D modeling. This section covers laser-based 3D scanners, recognized for their precision and field of view, and structured light scanners, which provide efficiency in capturing data. The distinction between contact and non-contact sensors will also be explored, highlighting their differing applications and benefits, ensuring users are well-informed about warranty and phase considerations in their selection process.
Laser-Based 3D Scanners
Laser-based 3D scanners utilize laser technology to capture precise measurements and generate high-quality data for inspection and modeling purposes. These scanners emit laser beams that reflect off surfaces, creating a detailed point cloud that represents an object’s geometry. The data is then processed using advanced software tools, allowing users to save the resulting models in various file formats for applications ranging from quality control to reverse engineering.
- Laser-based 3D scanners capture precise measurements.
- They generate high-quality data for inspection and modeling.
- The resulting models can be saved in various file formats.
Structured Light Scanners
Structured light scanners are instrumental in capturing precise three-dimensional measurements by projecting a series of light patterns onto an object. This technology enables the generation of accurate point clouds that represent the object’s surface geometry, making it essential for applications in various industries. Proper calibration of these scanners is crucial to ensure the accuracy of the measurements, allowing for reliable modeling and quality control in production processes.
Contact vs. Non-Contact Sensors
Contact sensors and non-contact sensors are two primary categories of industrial 3D scanning technologies, each serving distinct purposes based on their operational principles. Contact sensors require physical interaction with the object to gather measurement data, making them suitable for applications where high precision is essential, such as measuring complex geometries. In contrast, non-contact sensors utilize laser beams or structured light to capture data without touching the object, making them ideal for delicate materials or surfaces that cannot withstand physical contact while ensuring efficiency and rapid data acquisition.
Applications of Industrial 3D Scanning Sensors
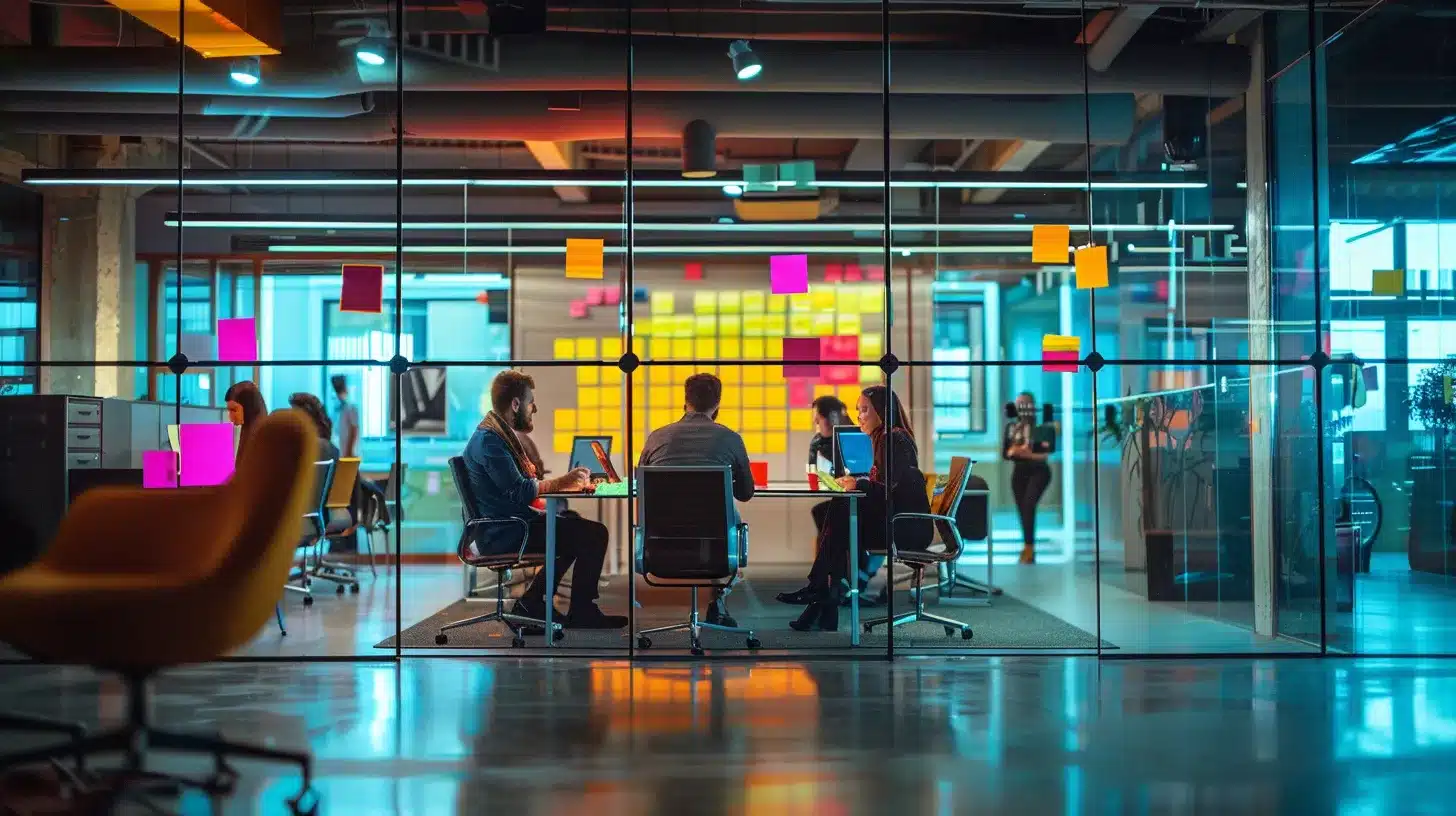
Industrial 3D scanning sensors play a significant role in various applications, enhancing quality control across manufacturing processes, supporting prototyping and product development, and facilitating reverse engineering. Additionally, these sensors provide precise inspection capabilities in the aerospace and automotive industries, ensuring adherence to stringent standards. Each application showcases the practicality and efficiency of 3D scanning technology in improving operational workflows.
Quality Control Across Manufacturing
Industrial 3D scanning sensors are pivotal in ensuring quality control across manufacturing processes by providing accurate and timely measurements of products. These sensors enable manufacturers to identify discrepancies in dimensions and tolerances, resulting in improved product consistency and reduced waste. With real-time inspection capabilities, industries such as aerospace and automotive can maintain strict adherence to quality standards, leading to enhanced customer satisfaction and lower production costs:
- Real-time dimensional inspection of products
- Improved consistency in manufacturing results
- Reduction in waste and rework through early detection of issues
- Enhanced customer satisfaction through quality assurance
- Streamlined workflows in various industrial applications
Prototyping and Product Development
In the field of prototyping and product development, industrial 3D scanning sensors play a crucial role in streamlining the design process. These sensors capture detailed measurements that facilitate the rapid creation of accurate prototypes, enabling designers to test and refine their products before full-scale production. By utilizing 3D scanning technology, companies can significantly reduce development time and costs, ultimately leading to products that better meet customer needs and expectations.
Reverse Engineering Processes
In reverse engineering processes, industrial 3D scanning sensors play a crucial role by enabling the accurate capture of complex geometries from existing objects. This technology allows engineers to create digital models that can be modified and replicated, facilitating improvements and innovations in product design. By providing precise measurements and detailed surface data, these sensors significantly enhance the efficiency of the reverse engineering workflow, ultimately leading to faster product development cycles and reduced costs for businesses.
Inspection in Aerospace and Automotive Industries
In the aerospace and automotive industries, industrial 3D scanning sensors are integral to inspection processes, ensuring that components meet stringent quality standards. These sensors facilitate precise measurement of parts, enabling manufacturers to detect even minor discrepancies that could affect performance or safety. By implementing real-time inspection capabilities, companies can promptly address issues, leading to enhanced product reliability and compliance with industry regulations:
- Ensures compliance with aerospace and automotive standards.
- Facilitates precise measurement of complex components.
- Promotes early detection of quality issues, reducing potential risks.
Benefits of Using Industrial 3D Scanning Sensors
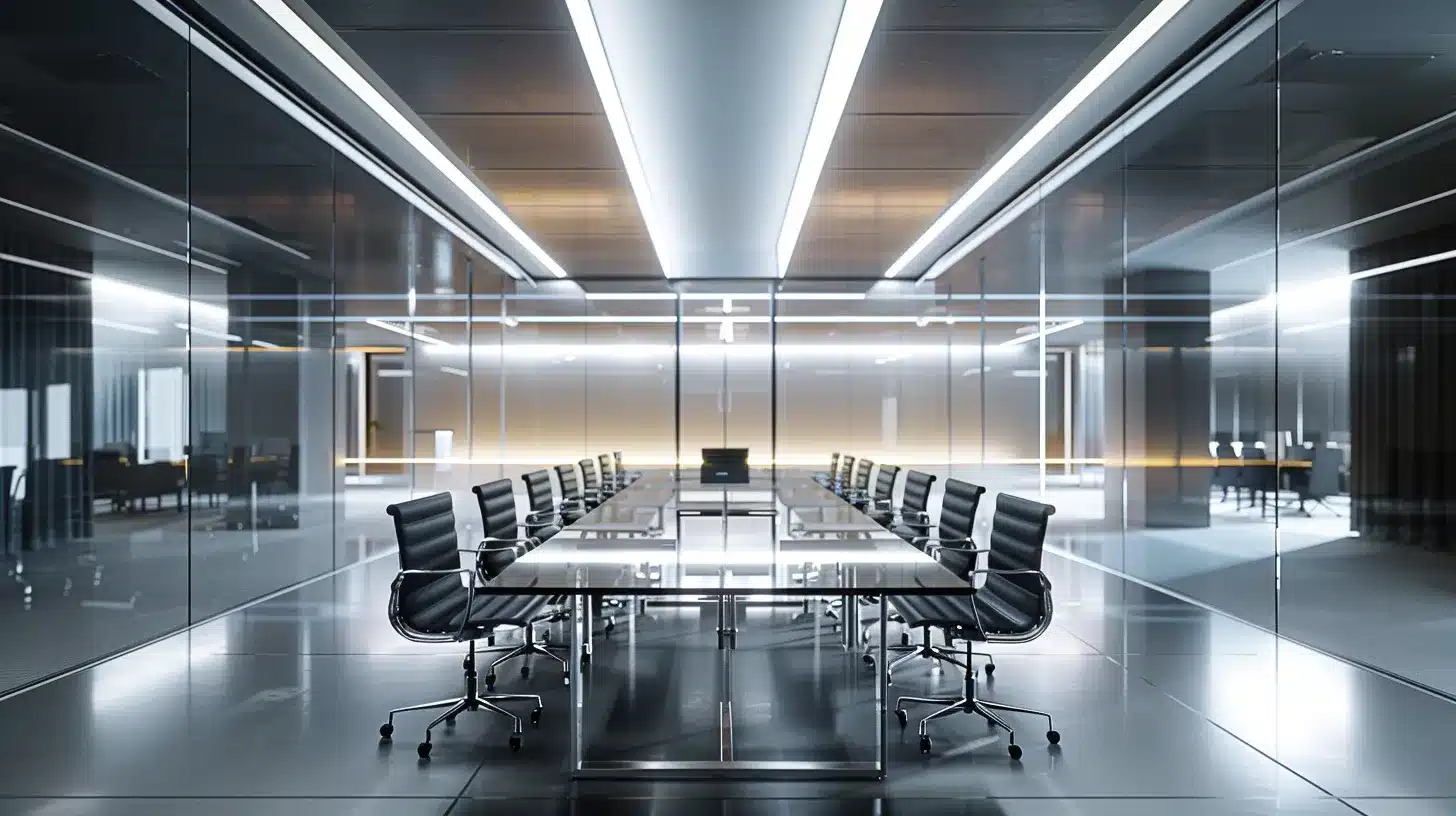
Industrial 3D scanning sensors offer enhanced accuracy and precision in capturing geometric data, which significantly impacts production quality. They contribute to improved efficiency by streamlining workflows, while also being cost-effective over time through reductions in waste and rework. Each of these benefits supports businesses in achieving better operational outcomes and meeting demanding standards.
Enhanced Accuracy and Precision
Enhanced accuracy and precision are among the standout advantages offered by industrial 3D scanning sensors, making them indispensable in modern manufacturing and engineering processes. By utilizing advanced technology like structured light and laser scanning, these sensors capture minute details and complex geometries, which significantly reduces the likelihood of errors in measurements. For instance, precise data collection is critical for applications such as quality control and reverse engineering, where even the smallest discrepancies can lead to major production issues. This level of accuracy not only ensures a higher-quality output but also promotes greater customer satisfaction and trust in the final products.
Improved Efficiency in Production
Improved efficiency in production is a significant advantage of utilizing industrial 3D scanning sensors. These tools facilitate rapid data acquisition, allowing manufacturers to quickly obtain precise measurements of components, which streamlines the workflow and reduces lead times. For example, by integrating 3D scanning technology into the design phase, companies can identify and address potential design flaws early, ultimately leading to faster iterations and improved overall productivity in the manufacturing process.
Cost-Effectiveness Over Time
Cost-effectiveness over time is a significant advantage of utilizing industrial 3D scanning sensors. By enabling quick and accurate data capture, these sensors minimize the need for rework and reduce material waste, ultimately leading to savings in both time and budget. For example, companies that integrate 3D scanning into their production processes often find that the initial investment is offset by enhanced operational efficiency and improved product quality, ensuring a better return on investment as projects evolve.
Selecting the Right Industrial 3D Scanning Sensor
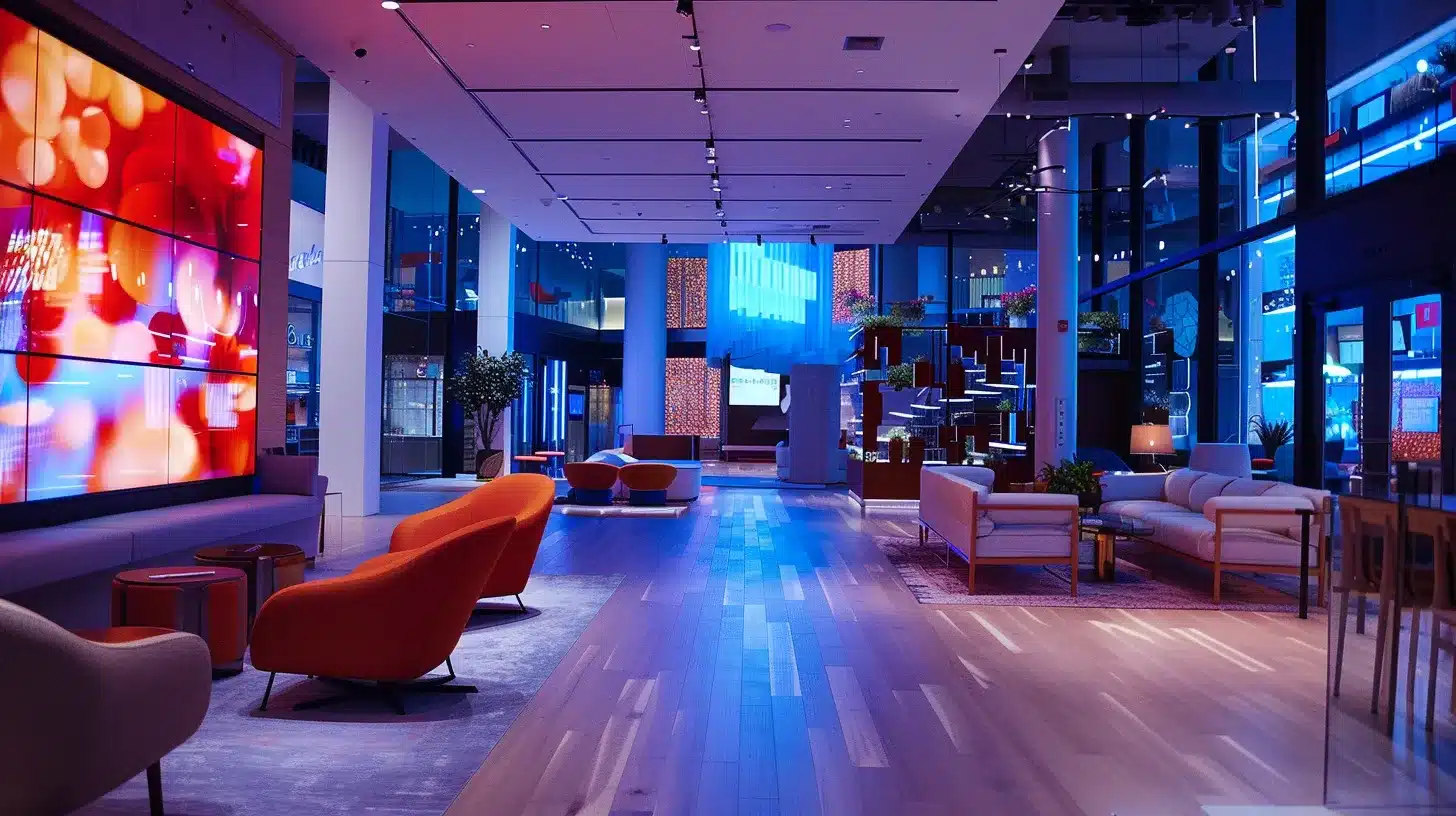
Selecting the appropriate industrial 3D scanning sensor involves evaluating several critical factors. First, users should consider performance and features, such as accuracy and scanning speed. Next, it’s essential to assess specific industry needs to ensure the chosen sensor aligns with distinct operational requirements. This section will provide insights into these factors, aiding informed decision-making.
Factors to Consider in Your Selection
When selecting an industrial 3D scanning sensor, several critical factors should be taken into account. Performance characteristics, such as accuracy and scanning speed, play a vital role in determining the effectiveness of the sensor for specific applications. Additionally, considering the environmental conditions in which the sensor will operate, along with the types of materials being scanned, ensures that users invest in technology tailored to their unique needs and operational demands:
- Assess performance characteristics like accuracy and scanning speed.
- Consider environmental conditions for optimal functionality.
- Evaluate materials to ensure compatibility with the sensor technology.
Comparing Performance and Features
When comparing performance and features of industrial 3D scanning sensors, it is essential to evaluate factors such as measurement accuracy, scanning speed, and usability. A sensor’s ability to deliver precise measurements, particularly in challenging industrial environments, can significantly impact applications like quality control and product development. For instance, sensors that offer higher resolution and faster data acquisition can enhance efficiency in manufacturing workflows, ultimately contributing to improved outputs and reduced costs.
Assessing Specific Industry Needs
Assessing specific industry needs is essential for selecting the right industrial 3D scanning sensor, as different sectors require tailored solutions to meet their unique operational challenges. For instance, the aerospace industry often demands incredibly precise measurements to ensure component reliability, while automotive manufacturers prioritize speed and efficiency in their workflows. By understanding these distinct requirements, organizations can choose sensors that not only align with their quality assurance standards but also enhance productivity and streamline their processes.
Future Trends in Industrial 3D Scanning Technology
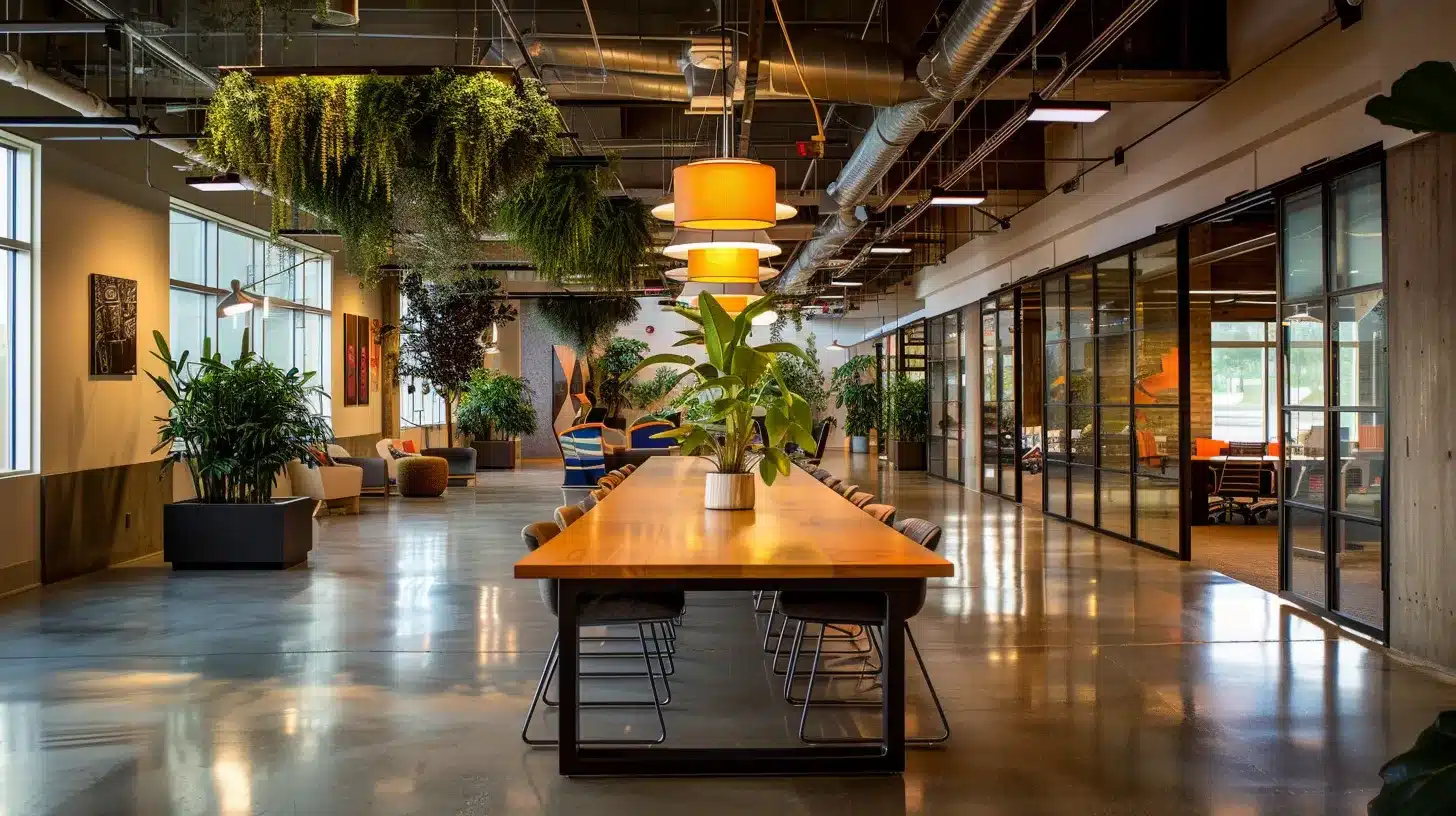
The future of industrial 3D scanning technology is shaped by key advancements that enhance its efficacy and applicability. Integration with artificial intelligence is set to improve data analysis and decision-making processes. Advancements in sensor design and software development promise more reliable and detailed measurements. Furthermore, the role of automation in 3D scanning will streamline operations, leading to faster workflows and heightened productivity across various industries.
Integration With Artificial Intelligence
The integration of artificial intelligence in industrial 3D scanning technology stands to significantly enhance the accuracy and efficiency of data analysis. AI algorithms can process large volumes of scanning data swiftly, allowing for real-time insights into geometric variations and potential design flaws. These advancements empower industries to refine their quality control processes and make informed decisions faster, contributing to improved productivity and reduced downtime.
- AI enhances data processing efficiency.
- Real-time insights into geometric variations.
- Improves quality control processes.
- Facilitates faster decision-making.
- Increases overall productivity and reduces downtime.
Advancements in Sensor Design and Software
Recent advancements in sensor design and software have significantly enhanced the capabilities of industrial 3D scanning sensors, resulting in greater accuracy and efficiency. Innovations such as improved algorithms and faster processing speeds allow for quicker data acquisition and analysis, enabling users to capture high-resolution models with minimal downtime. For example, the integration of machine learning in software facilitates better pattern recognition, leading to more reliable dimensional inspections that support various industries in maintaining quality standards.
The Role of Automation in 3D Scanning
The role of automation in 3D scanning significantly enhances efficiency and precision across various industries. By integrating automated systems with industrial 3D scanning sensors, businesses can reduce manual intervention, leading to faster data collection and analysis. This advancement addresses common operational challenges, such as minimizing human error and increasing throughput, ultimately supporting more streamlined workflows:
- Automation reduces manual intervention in scanning processes.
- Increased speed in data collection enhances productivity.
- Minimized human error leads to higher accuracy in results.
- Streamlined workflows improve overall operational efficiency.